Start a Career That
Will Save the World
That’s a bold statement. And we believe it’s true. Because here, you’ll develop and expand our patented high-performance glass technologies that significantly reduce the energy used by buildings, creating the potential to affect climate change by dramatically lowering carbon emissions.
Start a Career That
Will Save the World
That’s a bold statement. And we believe it’s true. Because here, you’ll develop and expand our patented technologies that significantly reduce the energy used by buildings, creating the potential to affect climate change by dramatically lowering carbon emissions.
LuxWall was founded on our ability to See Beyond the global energy and environmental challenges of today.
Now, we’re looking for the people who will further develop and expand our products for global applications. We’re looking for you.
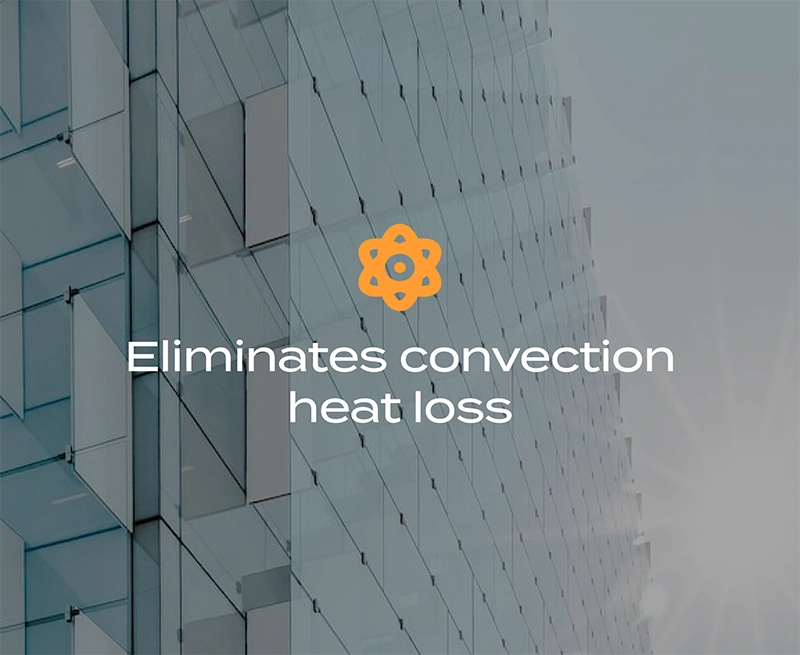
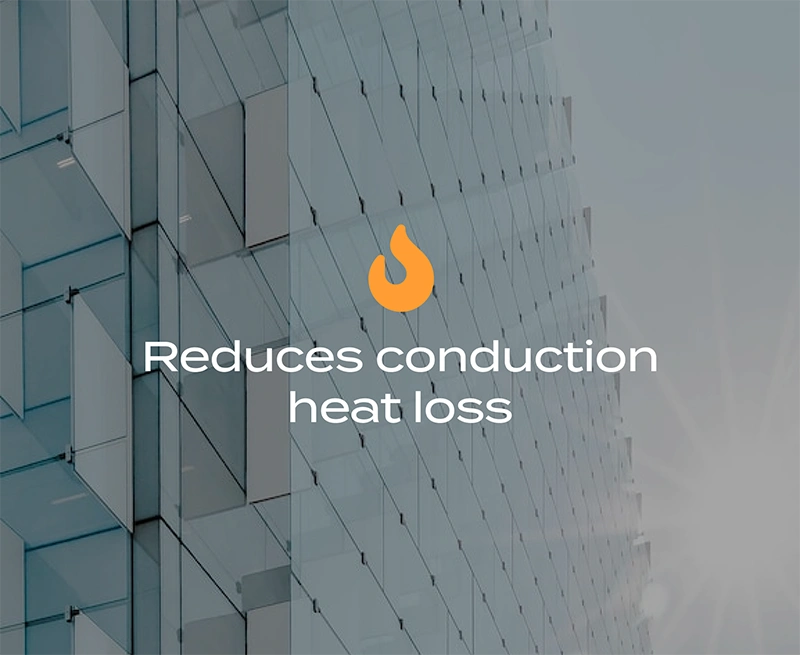
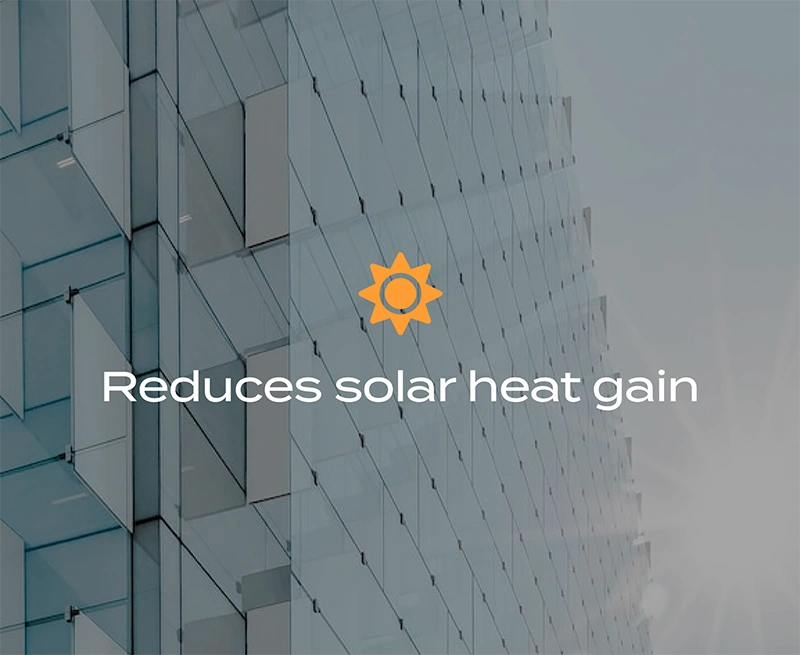
Saving the Planet Just Might be Your Destiny
Here, you’ll work hands-on with a first-to-market product in the industry – a patented new vacuum insulating glass technology that acts as transparent insulation for buildings. Our technological advancements in glass will accelerate us to net zero for buildings. And with mass adoption, LuxWall glass can reduce global carbon emissions by 14%.
Become an Essential Member
of a Meaningful Team
These are the values that guide us toward success every day. If this sounds inviting to you, let’s meet.
See Beyond
We see beyond what’s happened – and what’s coming. We see a portal to what’s possible, and a new instrument to dramatically reduce emissions. We see the power to connect humankind with a greater vision. We see a new era where all people across the planet are living more sustainable lives. Our purpose is clear. We are LuxWall. And we See Beyond.
Our Geniuses Love Their Jobs
Share in a thriving culture that celebrates individualism and diversity while fostering your personal achievement and success. Capitalize on the enthusiastic support of powerful venture capitalists, including Breakthrough Energy.
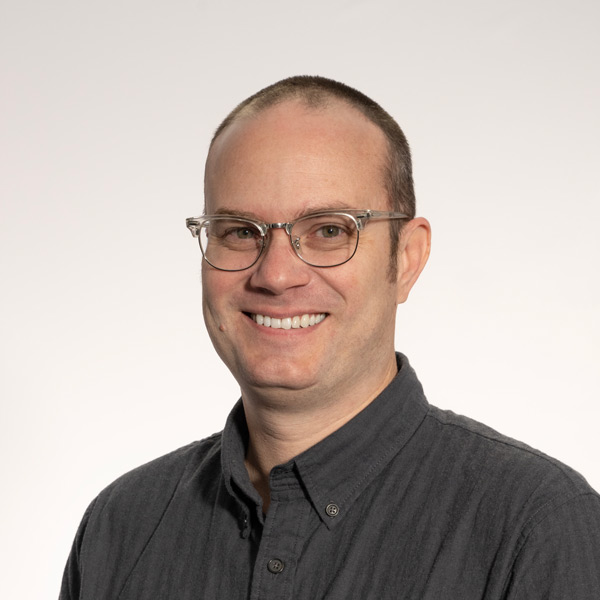
Christian Bischoff
Director of R&D
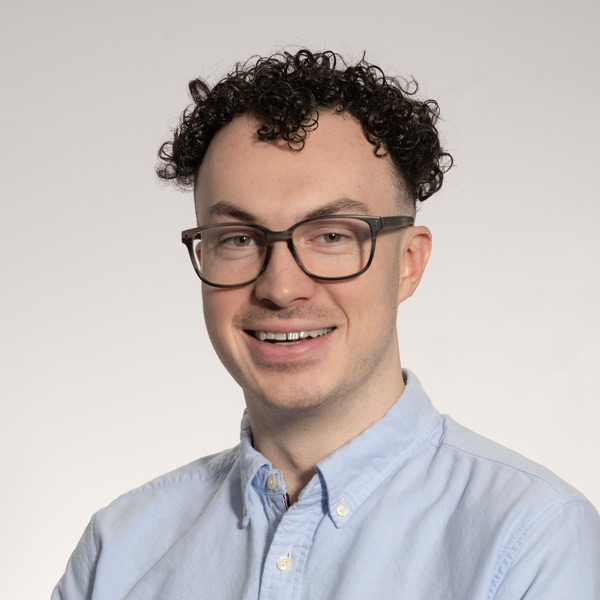
Riley Donahue
Ceramics Engineer
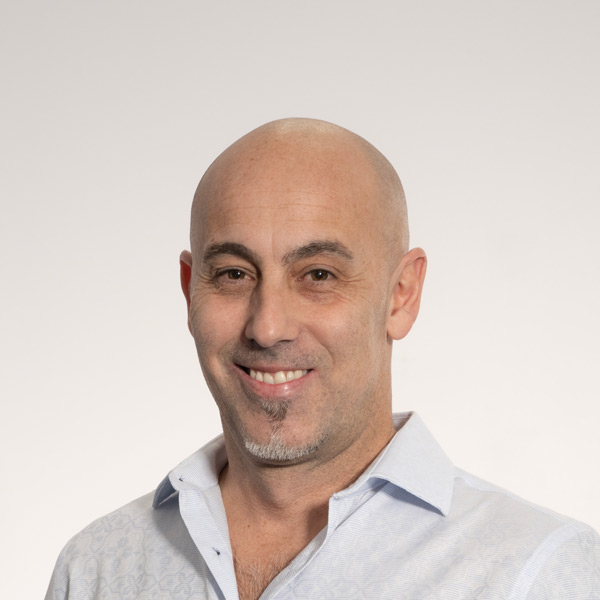
Maximo Frati
Senior Staff Engineer
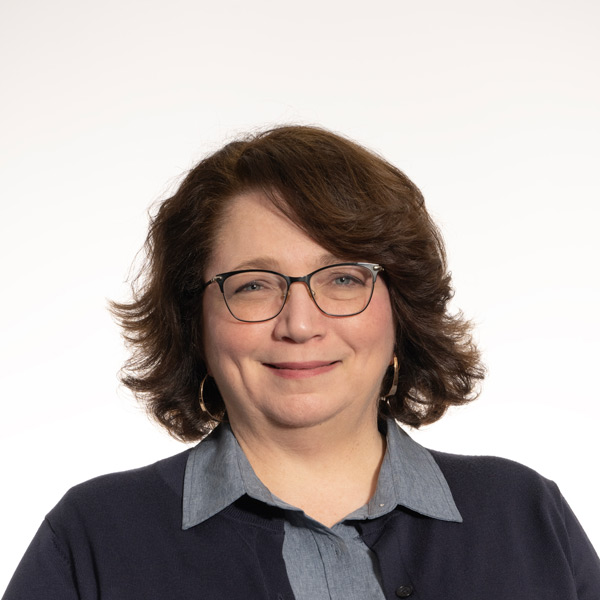
Lynda Navarre
Purchasing Manager
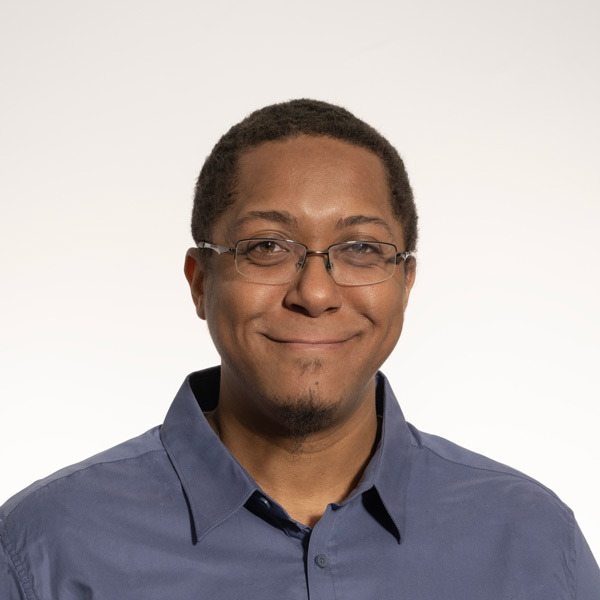
Shaun Jones
Test & Validation Engineer
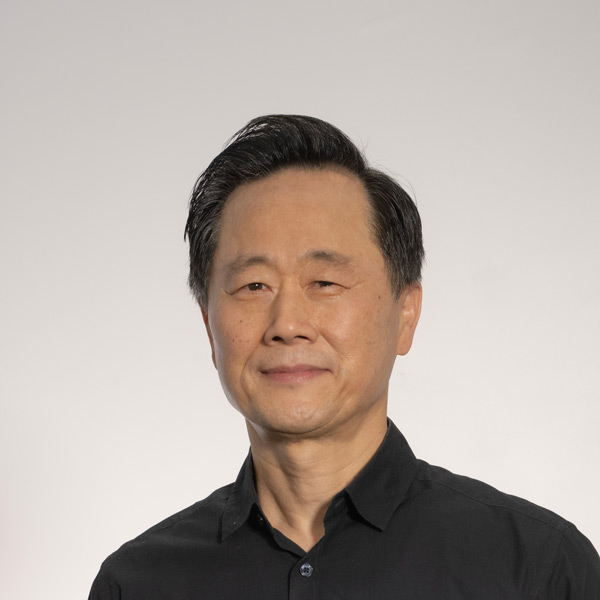
Jun Huh
Senior Staff Scientist
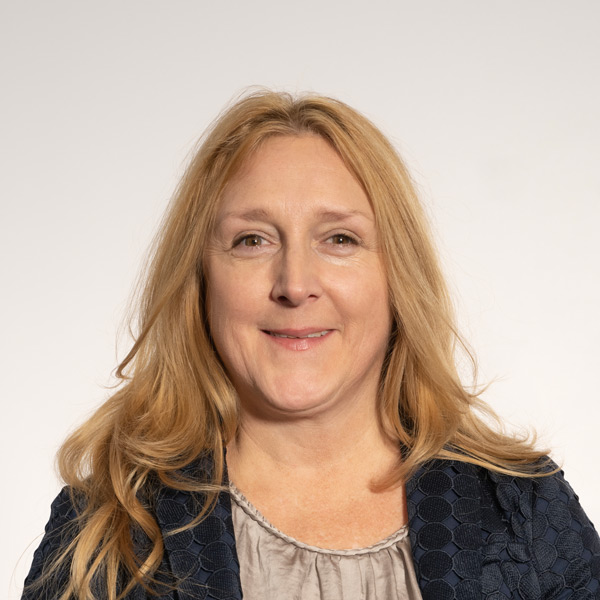
Jean Mayher
Vice President, Sustainability
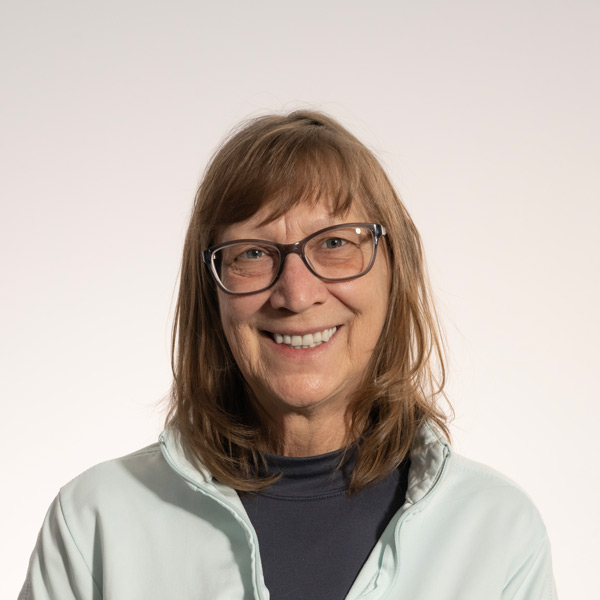
Ginger Pietka
Principal Engineer
Life-Changing Opportunities
80% of medical, dental and vision premiums covered for employees |
Health insurance coverage starts first day of the month following LuxWall date of hire if start date does not fall on the first of the month |
HMO, PPO or HSA medical plan and account options |
Employee Assistance Programs for employees provided by EmPower HR |
Twelve (12) company paid holidays and generous Paid Time Off policies |
80% of medical, dental and vision premiums covered for dependents |
12 weeks paid parental leave for the birthing parent and 4 weeks paid leave for the non-birthing parent |
Access to Dependent Care Account for Child Day Care or Adult Day Care |
Access to an Adoption Assistance Flexible Spending Account |
Access to Commuter Benefits Account with tax-free payments |
Employee stock options |
Finance and stock option education and tax advice provided by Carta |
Company-sponsored 401(k) through Schwab Financial Services with company match |
Employer-sponsored long-term disability and life insurance policies |
Company programs for personal and professional development |
Current Openings
LuxWall is focused on the product development, scaling, and commercializing of innovative glass products and solutions for the built environment. LuxWall’s transparent insulation technology, Enthermal, provides a step change in energy performance by significantly reducing convective, conductive, and radiative heat gain and heat loss in buildings. Acting as a transparent thermos bottle for buildings, LuxWall has the potential to reduce global carbon emissions by more than 0.5 gigaton per year with mass adoption. Enthermal will forever change the way buildings are designed and constructed for the future sustainability of our planet.
Role Overview:
The Vice President, Business Development (BD) reports directly to the CEO, leading Luxwall sales team, responsible for the direction and management of all business development planning and operations, including market competitiveness, pricing, distribution and channel strategy. A Vice President is a member of LuxWall senior staff and as such is also expected to present and communicate progress towards goals regularly at leadership meetings; actively identify and pursue new business opportunities; contribute ideas into the overall management and well-being of the company.
The Vice President Business Development is tasked with driving the growth of company’s business model; building and execution of sales strategies/budget aligned with corporate strategic goals, and development/expansion of new/existing customer bases. In execution of product and market business plans, he/she is charged with Business Development team tasking, resourcing, and guidance; then monitoring the results, quantifying the successes and shortfalls, and adjusting as needed.
This position requires intimate customer knowledge to support acquiring new customers, driving sales, and promoting our products and services. This position requires prior Business Development capture success, strong ability to engage customer with the latest technology practices, and prior sales leadership experience.
Position Responsibilities:
- Direct development and execution of the business development vision, strategy, and processes that will increase revenue and profitability, expand markets, and accomplish key strategic and financial objectives.
- Create, administer and implement winning business development strategies that the company should pursue to meet short-, medium-, and long-term business objectives.
- Oversee company market research for optimizing go-to-market strategies including segments, sub-segments, applications, channels, and customers.
- Generate market and business analysis tools that enable the company maximize cash flow and ROI.
- Maintain and update market segmentation analyses on a regular basis to ensure the company is making sound business decisions relative to product(s), service(s), asset deployment, and financing.
- Collaborate with sales, marketing, and finance to understand price setting mechanisms, channel pricing models, profit strategies, and market strategies to maximize profit, cash flow and ROI, and build LuxWall internal tools to enable the company to make sound pricing decisions.
- Lead, while partnering with the CEO and other members of the leadership team, the review and exploration of new growth business strategies.
- Identify and evaluate new market segments, strategic partners, go-to-market channels and customers to grow company revenue and profit.
- Collaborate with marketing, sales, product development, finance, operations, and other stakeholders to support business development plans.
- Work with the CEO and the leadership team to establish a comprehensive strategic roadmap and implement initiatives to drive business results, and to provide fact-based thought leadership on key strategic and financial decisions.
- Develop, propose, gain approval, and oversee global growth efforts combining LuxWall assets, joint ventures, and licensing to maximize company valuation.
- Conduct financial feasibility studies collaborating with the CFO and develop proposals for new business opportunities including joint development agreements, joint marketing agreements, channel partnerships, and business partnerships.
- Oversee company energy and carbon modeling efforts to quantify the end user benefits and impacts of LuxWall products and correlate energy and carbon impact to end user payback/ROI and LuxWall’s price setting mechanism.
- Collaborate with sales, marketing and product development to define requirements for channel energy and carbon calculator tools and oversee the design, development and implementation of the tools to the required target audiences. Fully integrate into the company operating models.
- Implement metrics and measure results to ensure company goals are achieved.
Qualifications:
- Bachelor’s degree in business, marketing, or a related field; MBA or advanced degree preferred.
- Proven track record of at least 10 years in business development, with a minimum of 5 years in a leadership role.
- Deep industry knowledge and an extensive network of industry contacts.
- Strong strategic thinking and analytical skills, with the ability to identify and prioritize growth opportunities.
- Exceptional negotiation and contract management skills.
- Ability to work independently and as part of a team.
- Leadership experience, with the ability to inspire and motivate teams to achieve objectives.
- Ability to adapt to a dynamic business environment and make data-driven decisions..
- Willingness to travel as required to establish and maintain business relationships..
Work Environment
- 100% Plant floor (PPE required)
-
Requires working in a fast-paced manufacturing environment with exposure to machinery, chemicals, and varying temperatures and noise levels.
- Constant communication with employees, peers and management
- Overtime as required
- Frequent requirement of handling heavy equipment (operation)
- Frequent need to give concentrated attention to surroundings
LuxWall, Inc. is an Equal Opportunity Employer. We do not discriminate based on race, color, religion, sex, sexual orientation, gender identity, national origin, disability, age, veteran status, or any other legally protected characteristics. All employment decisions are based on qualifications, merit, and business needs.
All applicants must complete and pass a drug screening and background check. LuxWall’s process is a 10-panel drug screen which includes marijuana.
Join Our Team as a Production Supervisor – Second Shift
Location: Litchfield, MI
Reports to: Plant Manager
Department: Operations
Job Type: Full-Time, Onsite in Litchfield
At LuxWall, we pride ourselves on innovation and excellence in our industry. We are committed to optimizing our processes to deliver high-quality products and services to our customers. We are currently seeking a skilled and motivated Production Supervisor to join our team and drive continuous improvement in our operations.
LuxWall is focused on the product development, scaling and commercializing of innovative glass products and solutions for the built environment. LuxWall’s transparent insulation technology, Enthermal Glass, provides a step change in energy performance by significantly reducing convective, conductive, and radiative heat gain and heat loss in buildings. Acting as a transparent thermos bottle for building, LuxWall has the potential to reduce global carbon emissions by more than 0.5 gigaton per year with mass adoption. Enthermal Glass will forever change the way buildings are designed and constructed for the future sustainability of our plant.
Job Summary:
The Production Supervisor is responsible for managing and coordinating the activities of the production team to meet production goals and quality standards. This role involves supervising staff, ensuring safety regulations are followed, optimizing workflows, and maintaining production schedules.
Key Responsibilities:
- Lead, mentor, and supervise production workers, ensuring efficient work practices.
- Assign tasks to production workers based on production schedules and skill levels.
- Monitor employee performance and provide feedback, training, and support as needed.
- Foster a positive work environment by promoting teamwork and addressing conflicts
- Ensure that production processes run smoothly and efficiently.
- Implement and enforce quality control procedures to minimize defects and waste.
- Work closely with the Quality Assurance team to address any quality issues.
- Ensure that all production activities comply with company safety policies and regulations.
- Conduct regular safety inspections and enforce the use of personal protective equipment (PPE).
- Promote a culture of safety and ensure all employees are trained on safety procedures.
- Maintain accurate production records, including shift reports, production logs, and employee attendance.
- Report on production metrics, including output, efficiency, and quality.
- Provide regular updates to the Production Manager on production progress and challenges.
- Identify opportunities for process improvements and implement solutions.
- Participate in lean manufacturing initiatives and continuous improvement projects.
- Collaborate with the engineering and maintenance teams to enhance production processes.
- Manage the inventory of raw materials, tools, and equipment needed for production.
- Coordinate with the supply chain or procurement teams to ensure timely availability of resources.
- Minimize downtime by ensuring equipment is well-maintained and ready for use.
Qualifications:
- High school diploma or equivalent (required).
- Associate degree in industrial engineering, manufacturing engineering or at least 3 years manufacturing/production experience.
- 5 years of experience in a manufacturing or production environment.
- 5 years of supervisory or managerial experience
- Experience with advanced automation technology.
- Strong leadership and team management skills.
- Excellent problem-solving and decision-making abilities.
- Good communication and interpersonal skills.
- Ability to work in a fast-paced environment and manage multiple priorities.
- Knowledge of production management software and Microsoft Office Suite.
- Excellent hands-on problem-solving skills and the ability to work independently or as part of a team.
- Ability to stand for long periods and perform physical tasks such as lifting, bending, and reaching.
- Willingness to work in a manufacturing environment with exposure to noise, heat, and machinery.
- The role involves working in a manufacturing facility, which may involve exposure to various environmental factors such as noise, dust, and temperature variations.
- The position may require shift work, including nights, weekends, and holidays.
What We Offer:
- Competitive Salary: Competitive salary and performance-based bonus
- Benefits Package: Comprehensive benefits including health insurance, 401K, paid time off and holidays.
- Professional Development: Opportunities for training, certification, and career advancement.
- Innovative Environment: Work with cutting-edge automation technology and processes.
- Supportive Culture: A collaborative and inclusive work environment that values diversity.
All applicants must complete and pass a drug screening and background check. LuxWall’s process is a 10-panel drug screen which includes marijuana.
LuxWall is focused on the product development, scaling, and commercializing of innovative glass products and solutions for the built environment. LuxWall’s transparent insulation technology, Enthermal™, provides a step change in energy performance by significantly reducing convective, conductive, and radiative heat gain and heat loss in buildings. Acting as a transparent thermos bottle for buildings, LuxWall has the potential to reduce global carbon emissions by more than 0.5 gigaton per year with mass adoption. Enthermal™ will forever change the way buildings are designed and constructed for the future sustainability of our planet.
The Second Shift Manufacturing Technician will be responsible for operating and maintaining production machinery and equipment in a fast-paced manufacturing environment. You will be responsible for ensuring the efficient and safe production of high-quality products while adhering to established production standards and procedures.
Position Responsibilities
- Ability to record data and recognize via SPC analysis whether a process is in or out of control.
- Quality checks with data input into the Quality System to keep the process running efficiently.
- Set-up and adjust equipment settings to meet production specifications and quality standards.
- Including navigation of HMI interface screens when powering up, troubleshooting, or operating automated equipment within the process.
- Conduct regular inspections and quality checks to ensure WIP & final products are conforming
- Identify and resolve equipment malfunctions or operational issues in a timely manner, collaborating with Maintenance Technicians, Process Engineers and Control Engineers.
- Perform routine maintenance tasks, such as cleaning, lubricating, and minor repairs, to keep equipment in optimal condition.
- Accurately record production data, equipment maintenance logs, and other relevant information.
- Understand and follow work instructions and control plans.
- Adhere to all company safety policies and procedures.
- Identify opportunities for process improvement and efficiency enhancement, suggesting ideas and participating in implementation efforts.
- Participate in training programs to enhance skills and knowledge of equipment operation, safety procedures and production techniques.
- Understanding trends on reliability and yield.
- Assist with other key tasks during changeovers.
- Possess the ability to learn in a high velocity environment to enable themselves to become flexible and fluent in the operation of multiple machine types. (“Quick Study” & “Multi-tasker”)
- Other duties as assigned.
Position Requirements:
- High school diploma or equivalent required. Technical or vocational training in a manufacturing or a related field is beneficial.
- Associate or Bachelor Degree in Electrical Engineering, Automation, Control Systems, or a related field, beneficial.
- 3-5 years working in a manufacturing environment required.
- Experience reading blueprints and maintaining strict product standards.
- Experience with operation of robotics and high-precision gantry systems.
- Experience with machine vision systems.
- Strict adherence to Standard Work Instructions with a focus on quality control.
- Proven experience as a production operator or similar role in a manufacturing environment.
- Strong mechanical and technical aptitude with the ability to operate and troubleshoot production machinery effectively.
- Ability to interpret technical manuals, diagrams, and instructions.
- Experience operating equipment via an HMI.
- Willingness to work in shifts and adapt to changing production schedules.
- Exceptional attention-to-detail and a high sense of urgency.
- Ability to stand frequently, walk, kneel, and bend.
- Physical strength to manage demands such as lifting heavy objects (50 lb. Minimum).
- Effective communication skills, both verbal and written, to interact with team members, contractors, and employees.
- Ability to work independently and prioritize tasks in a fast-paced environment.
- Glass manufacturing experience is a plus.
- Proficiency in forklift operation is a plus.
- **Second shift signing bonus of $ 1,000 upon completion of 30 days of employment**
- **Shift premium available for second shift.**
All applicants must complete and pass a drug screening and background check. LuxWall’s process is a 10-panel drug screen, which includes marijuana.
LuxWall is focused on the product development, scaling, and commercializing of innovative glass products and solutions for the built environment. LuxWall’s transparent insulation technology, Enthermal™, provides a step change in energy performance by significantly reducing convective, conductive, and radiative heat gain and heat loss in buildings. Acting as a transparent thermos bottle for buildings, LuxWall has the potential to reduce global carbon emissions by more than 0.5 gigaton per year with mass adoption. Enthermal™ will forever change the way buildings are designed and constructed for the future sustainability of our planet.
A Quality Systems Engineer is a professional who ensures that all products within a company meet consistent standards. They develop and implement quality control tests to ensure the company’s production processes yield the desired result, inspecting at various production stages and writing reports on their findings to act where needed.
Position Responsibilities
- Create quality documents in compliance with the company’s quality system standards.
- Responsible for troubleshooting root cause analysis, SPC data analysis, implementation and maintaining up to date documentation related to APQP, PFMEA, DFMEA and control plans.
- Maintain SPC charts and ensure they are within capability range. Develop resolution for out of spec. data.
- Investigate root causes of quality problems and implement corrective actions. Work closely with production and engineering teams to address and resolve quality issues.
- Participate and coordinate Advanced Product Quality Planning (APQP)
- Lead and conduct the improvement of capability studies and gauge Repeatability and Reproducibility (R & R) analysis.
- Establish quality standards for products and processes in collaboration with engineering and production teams.
- Design and develop testing methods and equipment.
- Inspect raw materials, components, and final products to ensure they meet quality standards. <liConduct routine and non-routine analysis of product quality. Review and make recommendations for the disposition of non-conforming/suspect products in a timely manner and ensure formal corrective actions are answered within customers guidelines.
- Ensure all regulatory and industry standards required testing, reporting and recordkeeping is completed as required.
- Contribute and assist in variability reduction, process improvement and continuous improvement.
- Participate in training programs to enhance skills and knowledge of equipment operation, safety procedures and production techniques.
- Contribute to successful project completion by participating in the resolution of issues such as conflicting design requirements, safety concerns, unsuitability of standard material and difficult coordination requirements.
- Ensure time management is executed in the completion of all projects/duties.
- Assist with the needs of the customer in internal functions in addressing quality system requirements.
- Track customer satisfaction measurable and communicate to appropriate personnel and/or management.
- Oversee the evaluation of process audits and finished product inspections for quality and reliability.
- Ensure effective quality training for all team members.
- Communicate significant quality issues throughout all levels of the Company.
- Work closely with other managers to address the day-to-day problems and improve product/process quality.
- Prepare and distribute daily, weekly, monthly/annual reports depicting the Key Performance Indicators and progress toward targets. Submit detailed reports to appropriate leadership team personnel.
- Devise and review specifications for products or processes.
- Set requirements for raw material or intermediate products for suppliers and monitor their compliance.
- Ensure adherence to health and safety guidelines as well as legal obligations.
- Inspect final output and compare properties to requirements.
- Present continuous improvement opportunities for and develop new efficient procedures.
- Other duties as assigned.
Position Requirements:
- Bachelor’s Degree in Quality Engineering, Mechanical Engineering, Industrial Engineering or related technical field required, with three to five years relevant Quality Engineering, experience required preferably in a manufacturing environment.
- Lead Auditor preferred.
- Working knowledge of Lean Manufacturing, 5-S, Total Quality Concepts, and Six Sigma.
- Hands-on approach to problem solving and analysis.
- Excellent Data Analytical Skills.
- Ability and willingness to uphold the Company Values of Safety, Customer Focused, Teamwork, Excellence and Trust.
All applicants must complete and pass a drug screening and background check. LuxWall’s process is a 10-panel drug screen, which includes marijuana.
Join Our Team as a Production Scheduler
Location: Jackson, MI
Reports to: Supply Chain Manager
Department: Operations
Job Type: Full-Time, Onsite
At LuxWall, we pride ourselves on innovation and excellence in our industry. We are committed to optimizing our processes to deliver high-quality products and services to our customers. We are currently seeking a skilled and motivated Plant Manager to join our team and drive continuous improvement in our operations.
LuxWall is focused on the product development, scaling and commercializing of innovative glass products and solutions for the built environment. LuxWall’s transparent insulation technology, Enthermal Glass, provides a step change in energy performance by significantly reducing convective, conductive, and radiative heat gain and heat loss in buildings. Acting as a transparent thermos bottle for building, LuxWall has the potential to reduce global carbon emissions by more than 0.5 gigaton per year with mass adoption. Enthermal Glass will forever change the way buildings are designed and constructed for the future sustainability of our plant.
Job Summary:
The Production Scheduler is responsible for planning, organizing, and coordinating the production schedule to ensure efficient and timely manufacturing processes. This role involves working closely with production, supply chain, and quality control teams to balance demand with production capacity, minimize downtime, and ensure that products meet quality standards. The ideal candidate will have strong analytical skills, experience in production planning, and a deep understanding of the manufacturing processes in the glass industry.
Key Responsibillties
- Develop and maintain detailed production schedules based on customer orders, inventory levels, and production capacity.
- Monitor and adjust schedules as necessary to accommodate changes in demand, production delays, or equipment issues.
- Coordinate with the supply chain team to ensure timely availability of raw materials and components required for production.
- Analyze production capacity and identify potential bottlenecks or constraints.
- Work with production managers to optimize equipment usage and workforce allocation.
- Implement strategies to maximize production efficiency and minimize downtime.
- Liaise with production, quality control, and logistics teams to ensure smooth workflow and on-time delivery of finished products.
- Communicate production schedules and any changes to relevant departments and stakeholders.
- Address and resolve any scheduling conflicts or issues that may arise during the production process.
- Monitor inventory levels of raw materials and finished goods, ensuring alignment with production schedules.
- Work with procurement to manage lead times and order quantities to avoid production delays.
- Conduct regular inventory audits and adjust production plans as necessary to optimize stock levels.
- Analyze production data to identify trends, inefficiencies, and areas for improvement.
- Prepare and present reports on production performance, schedule adherence, and inventory status to management.
- Utilize production scheduling software and tools to track and manage production activities.
- Identify opportunities to improve production scheduling processes and enhance overall operational efficiency.
- Implement best practices in production scheduling and participate in continuous improvement initiatives.
- Stay updated with industry trends, technologies, and methodologies relevant to production scheduling in the glass industry.
Qualifications:
- Bachelor’s degree in Industrial Engineering, Manufacturing Engineering, Operations Management, or a related field.
- Minimum of 3-5 years of experience in production scheduling, planning, or a similar role within the manufacturing industry.
- Experience with production scheduling software and tools (e.g., SAP, ERP systems, MRP systems).
- Strong analytical and problem-solving skills, with the ability to manage complex schedules and adapt to changes.
- Excellent organizational and time-management skills, with attention to detail.
- Proficiency in Microsoft Office Suite (Excel, Word) and experience with data analysis tools.
- Strong communication and interpersonal skills for effective collaboration across departments.
- Knowledge of lean manufacturing principles and practices is a plus.
- Competitive Salary: Competitive salary and performance-based bonus
- Benefits Package: Comprehensive benefits including health insurance, 401K, paid time off and holidays.
- Professional Development: Opportunities for training, certification, and career advancement.
- Innovative Environment: Work with cutting-edge automation technology and processes.
- Supportive Culture: A collaborative and inclusive work environment that values diversity.
What We Offer:
All applicants must complete and pass a drug screening and background check. LuxWall’s process is a 10-panel drug screen which includes marijuana.
LuxWall is focused on the product development, scaling, and commercializing of innovative glass products and solutions for the built environment. LuxWall’s transparent insulation technology, Enthermal, provides a step change in energy performance by significantly reducing convective, conductive, and radiative heat gain and heat loss in buildings. Acting as a transparent thermos bottle for buildings, LuxWall has the potential to reduce global carbon emissions by more than 0.5 gigaton per year with mass adoption. Enthermal will forever change the way buildings are designed and constructed for the future sustainability of our planet.
The Supply Chain Manager is the leader overseeing the manufacturing supply chain from raw material supply to customer deliveries. Responsibility includes inside sales, customer order entry, production scheduling, logistics, customer deliveries, inventory and WIP management, raw material, MRO and spares purchasing and management, and inbound freight.
Position Requirements
- Collaborates with other departments and stakeholders to identify and maintain resources needed to establish and provide an effective supply chain.
- Establishes performance metrics for measurement, comparison, or evaluation of factors affecting the supply chain.
- Develops and maintains detailed inventories of materials and supplies located in the company, at sites, and in the factory.
- Analyzes current inventories and procedures; suggests improvements to increase efficiency of supply chain and profitability for the company.
- Develops policies to increase efficiency throughout the supply chain while ensuring quality and safety; implements subsequent changes to processes.
- Identifies optimal shipment and transportation routes with attention to consolidation of warehousing and distribution.
- Assesses the need for material-handling equipment and staffing; makes recommendations to ensure efficient loading, unloading, movement, and storage of materials.
- Negotiates prices for raw material and delivery with suppliers, vendors, and/or shipping companies.
- Participates as an advisory member of the product development team, providing information and guidance on availability and cost of supplies and materials.
- Acts as part of the team coordinating engineering changes, product line extension, or new product launches to ensure timely and orderly material and production flow transitions.
- Monitors the performance of suppliers, assessing their ability to meet quality and delivery requirements; identifies and qualifies new suppliers in collaboration with other departments.
- Ensure compliance with import/export regulations/customs regulations and legal and health and safety requirements.
- Performs other related duties as assigned.
Supervisory Responsibilities:
- Hires and trains departmental supervisors.
- Oversees the daily workflow and schedules of the department.
- Conducts performance evaluations that are timely and constructive.
- Handles discipline and termination of employees in accordance with company policy.
Position Requirements:
- Bachelor’s degree in business or related field required; master’s degree preferred.
- Three years of experience as a supervisor, manager, or similar relevant position required.
- Prior experience of working in logistics/supply chain/transportation function within the manufacturing environment with a comprehensive knowledge of logistics processes.
- High degree of knowledge and understanding of a variety of manufacturing, glass processes and components and of supply chain management.
- Strong IT systems knowledge, skills including knowledge, and understanding of specialist systems such as Enterprise Resource Planning (ERP), Bill of Material (BOM) and customer data systems.
- Fork truck qualified and capable of operating general heavy equipment including heavy loaded hoist.
- Strong interpersonal, negotiation and influencing skills.
- Excellent verbal and written communication skills.
- Excellent interpersonal and negotiation skills with a proven ability to create and maintain positive working relationships with vendors, suppliers, shippers, and customers.
- Strong supervisory and leadership skills.
- Excellent organizational skills and attention to detail.
- Thorough understanding of company products and logistics.
- Strong analytical and problem-solving skills.
- Proficient with Microsoft Office Suite or related software.
Work Environment
- 100% Plant floor (PPE required)
-
Requires working in a fast-paced manufacturing environment with exposure to machinery, chemicals, and varying temperatures and noise levels.
- Constant communication with employees, peers and management
- Overtime as required
- Frequent requirement of handling heavy equipment (operation)
- Frequent need to give concentrated attention to surroundings
Physical Demands
- Standing and Walking: The role requires standing and walking for extended periods, up to 8-12 hours per shift, depending on production demands.
- Lifting and Carrying: Must be able to lift and carry objects weighing up to [weight, e.g., 50 lbs.] regularly throughout the shift. Occasional lifting of heavier items may be required with assistance.
- Bending, Stooping, and Crouching: Frequent bending, stooping, crouching, and reaching are necessary to perform tasks such as machine operation, product assembly, and maintenance.
- Pushing and Pulling: The position involves pushing and pulling carts, tools, and materials weighing up to [weight, e.g., 100 lbs.], either manually or using appropriate equipment.
- Manual Dexterity: The ability to use hands and fingers to handle, control, or feel objects, tools, or controls with precision is required for operating machinery, assembling products, and performing maintenance.
- Climbing: Occasional climbing of ladders or steps to access equipment or storage areas may be required.
- Vision and Hearing: Adequate vision is necessary to read and interpret technical documents, operate equipment, and inspect products for quality. Adequate hearing is required to communicate effectively in a noisy environment and to be aware of machinery sounds for safety.
- Repetitive Motions: This job may involve repetitive hand, wrist, and arm motions during tasks such as assembling parts, operating equipment, or packaging products.
- Environmental Conditions: The role may require working in varying temperatures, including cold storage areas or areas where heat from machinery is present. Exposure to dust, chemicals, fumes, and loud noises is common in manufacturing environments, and appropriate personal protective equipment (PPE) must be worn.
- Physical Stamina: The job requires maintaining high energy levels and physical stamina to keep up with the pace of production and meet performance targets
LuxWall, Inc. is an Equal Opportunity Employer. We do not discriminate based on race, color, religion, sex, sexual orientation, gender identity, national origin, disability, age, veteran status, or any other legally protected characteristics. All employment decisions are based on qualifications, merit, and business needs.
All applicants must complete and pass a drug screening and background check. LuxWall’s process is a 10-panel drug screen which includes marijuana.
LuxWall is focused on the product development, scaling, and commercializing of innovative glass products and solutions for the built environment. LuxWall’s transparent insulation technology, Enthermal, provides a step change in energy performance by significantly reducing convective, conductive, and radiative heat gain and heat loss in buildings. Acting as a transparent thermos bottle for buildings, LuxWall has the potential to reduce global carbon emissions by more than 0.5 gigaton per year with mass adoption. Enthermal will forever change the way buildings are designed and constructed for the future sustainability of our planet.
The Second Warehouse and Packaging Associate will be responsible for the efficient operation of our warehouse facility. You will be responsible for various tasks related to receiving, storing, packaging, and shipping products ensuring accuracy, quality, and timely delivery. **Second shift signing bonus of $ 1,000 upon completion of 30 days of employment. Shift premium available for second shift.**
Position Responsibilities:
- Assemble and prepare products for shipment utilizing appropriate packaging materials based on product specifications and shipping requirements.
- Maintain efficiency of production to ensure timely assembly and shipment.
- Maintain proper storage of material and product inventory.
- Organize inventory in an easy-to-access process.
- Maintain the quality and upkeep of warehouse equipment including machinery, fixtures, and tools.
- Receive incoming shipments, inspect them for damages, and verify their accuracy against accompanying documentation.
- Sort, label, and store received goods in designated storage areas, ensuring proper organization and efficient space utilization.
- Operate warehouse equipment such as forklifts, pallet jacks, and hand trucks to move, stack, and transport materials, as necessary.
- Ensure the warehouse is clean and orderly.
- Collaborate with other team members to ensure smooth operations and customer satisfaction.
- Adhere to all company policies and procedures to maintain a safe working environment.
Position Requirements:
- High school diploma or equivalent.
- The ability to operate a forklift is a plus but will train if needed.
- SAP experience, preferred.
- Exceptional attention-to-detail and a high sense of urgency.
- Ability to stand frequently, walk, kneel, and bend.
- Physical strength to manage demands such as lifting heavy objects.
- Effective communication skills, both verbal and written, to interact with team members, contractors, and employees.
- Ability to work independently and prioritize tasks in a fast-paced environment.
- 100% Plant floor (PPE required).
- Requires working in a fast-paced manufacturing environment with exposure to machinery, chemicals, and varying temperatures and noise levels.
All applicants must complete and pass a drug screening and background check. LuxWall’s process is a 10-panel drug screen which includes marijuana.
LuxWall is focused on the product development, scaling, and commercializing of innovative glass products and solutions for the built environment. LuxWall’s transparent insulation technology, Enthermal, provides a step change in energy performance by significantly reducing convective, conductive, and radiative heat gain and heat loss in buildings. Acting as a transparent thermos bottle for buildings, LuxWall has the potential to reduce global carbon emissions by more than 0.5 gigaton per year with mass adoption. Enthermal will forever change the way buildings are designed and constructed for the future sustainability of our planet.
The Quality Control Technician will be responsible for ensuring that our products meet the highest standards of quality and reliability. In addition, you will be responsible for performing various tests, inspections, and analyses to assess product quality, identify defects or deviations from specifications, and recommend corrective actions.
Position Responsibilities
- Conduct quality control tests and inspections to verify compliance with quality standards and specifications.
- Utilize a range of testing equipment, tools, and instruments to perform accurate and reliable measurements and assessments.
- Analyze test data and inspection results to identify quality issues, defects, or deviations from established standards.
- Collaborate with cross-functional teams, to resolve quality-related issues and implement corrective actions.
- Maintain and update quality control documentation, including test reports, inspection records, and quality assurance procedures.
- Participate in the development and implementation of quality control processes, procedures, and guidelines to improve overall product quality and reliability.
- Train and educate production personnel on quality control procedures, standards, and best practices.
Position Requirements
- Associate degree in a maintenance or technical field preferred or at least 5 years manufacturing or industrial experience.
- Proven experience working in a quality control or quality assurance role, preferably in a manufacturing or production environment.
- Strong knowledge of quality control methodologies, tools, and techniques.
- Proficiency in using quality control testing equipment, tools, and software.
- Excellent analytical skills and exceptional attention-to-detail.
- Excellent problem-solving and decision-making skills.
- Effective communication skills, both verbal and written, to interact with team members, contractors, and employees.
- Ability to work independently and prioritize tasks in a fast-paced, deadline-driven environment.
All applicants must complete and pass a drug screening and background check. LuxWall’s process is a 10-panel drug screen which includes marijuana.